In gas transfer technology, innovation is pivotal in enhancing efficiency and sustainability. 3M™Liqui-Cel™EXF Series membrane contactors utilize technology that stands out as a game-changer. As we’ll discuss, the advantages achieved with this technology have redefined dissolved gas control in processes across various industries.
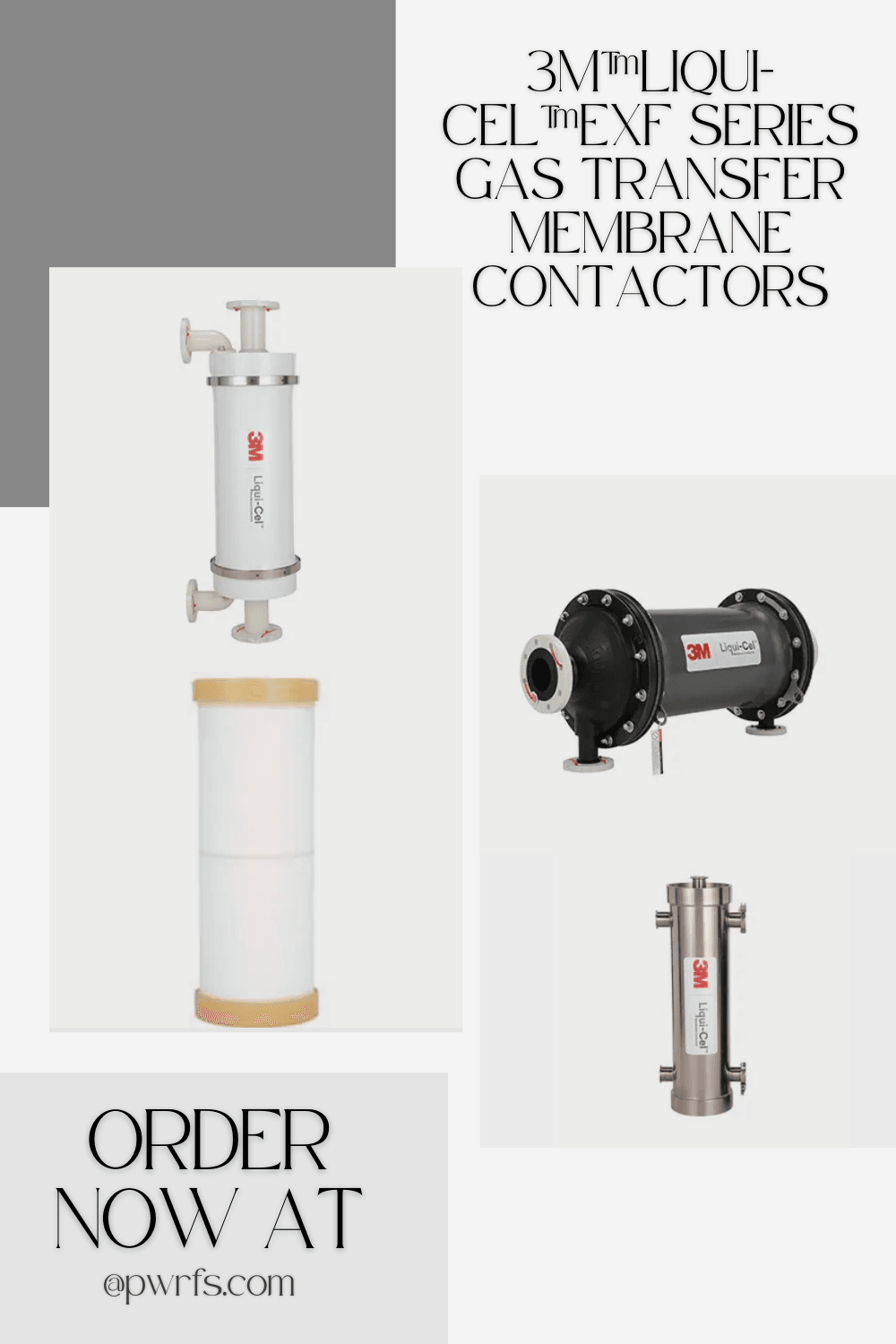
Efficiency at Its Best:
3M™Liqui-Cel™EXF Series membrane contactors have unique features that significantly improve the gas transfer efficiency with minimal energy consumption. Guided by a radial baffle, the fluid to be processed passes over the membrane’s surfaces twice before exiting the contactor. This improves the contact between the processed fluid and gas transfer surface qualitatively and quantitively. As a result, the gas transfer rate is increased and dissolved gas can be controlled more precisely. This reduces gas control systems’ size, complexity, energy consumption, and cost. Now, on-demand gas control is a reality. Achieving a targeted dissolved gas level is now as simple as turning on a faucet. Many customers have been able to reduce dissolved gas targets from 1 ppm down to <20 ppb while simplifying their operations.
Compact and Space-Saving Design:
Space constraints can be a significant challenge in various industrial settings. The compact design of the 3M™Liqui-Cel™EXF Series membrane contactor addresses this issue effectively. Its small footprint allows easy integration into existing systems, saving valuable floor space and simplifying installation.
Reliable and Low Maintenance:
Durability and reliability are paramount in industrial processes. The 3M™Liqui-Cel™EXF Series membrane contactor is built to last, with minimal maintenance requirements. Furthermore, systems incorporating Liqui-Cel contactors require minimal equipment with moving parts and controls. A system can be as simple as a single contactor but typically may have a vacuum generator and some valves. Simplicity ensures consistent performance while reducing operator attendance and maintenance needs. One of our customers had a time-consuming process of filling tanks and sparging for hours to deoxygenate water. This process was very laborious and inefficient. Now, they feed deaerated water directly from their Liqui-Cel DAW system to their process on demand. 3M™Liqui-Cel™EXF Series membrane contactors offer precise, on-demand dissolved gas control with a hassle-free design.
Versatile Applications:
3M™Liqui-Cel™EXF Series membrane contactors offer more versatility. They are adaptable to different processes and fluids because they are available in many sizes with material and configuration options. Sizes range from ½ to 14 inches in diameter and 1 to 80 inches in length. Available process connections include flanges, sanitary, pipe and tube fittings. Housing materials offered include polypropylene, ABS, FRP and stainless steel.
The options available in Liqui-Cel EXF series membrane contactors make them feasible for many use cases. Power generation plants use Liqui-Cel contactors for deoxygenating boiler feedwater and decarbonating RO feedwater. Beverage plants use them to produce deaerated water for mixing, bottle rinsing, and flushing equipment. Pharma companies incorporate deoxygenated water into products and intermediaries utilizing this technology.
The versatility of the 3M EXF Series membrane contactors is a key characteristic that differentiates them from other available options.
Conclusion:
3M™Liqui-Cel™EXF Series membrane contactors are a revolutionary technology transforming dissolved gas control across industries. Its efficiency, versatility, unmatched performance, compact, simple design, and reliability make it the preferred choice for businesses looking to speed up, simplify and improve the precision of degasification and gasification operations. By choosing a 3M™Liqui-Cel™ EXF Series gas control system, companies can elevate productivity and reduce operational costs while improving the quality of products and the reliability of their processes. Embrace the future of gas transfer with 3M’s innovative membrane contactor technology.